Sheet metal stamping and deep draw stamping are two commonly used manufacturing techniques in the production of metal parts. Both techniques involve the use of a metal sheet, but they differ in terms of their process and the final product they produce. In this post, we will explore the pros and cons of sheet metal stamping and deep draw stamping to help you understand which one is right for your specific manufacturing needs.
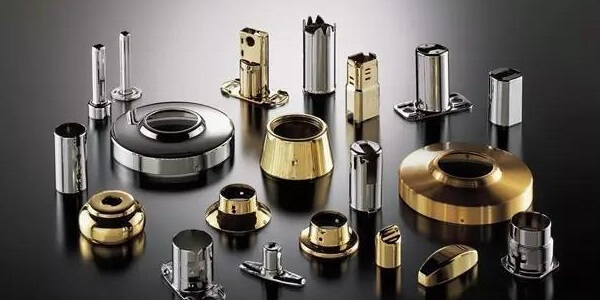
Sheet Metal Stamping
Sheet metal stamping is a process used to create flat or 3-dimensional parts by punching, cutting, or forming a metal sheet. This process is carried out using a stamping press, which applies pressure onto a metal sheet to create the desired shape. Some typical examples of sheet metal stamping include automotive parts, electronic enclosures, and aircraft components.
Pros of Sheet Metal Stamping
Efficient production: Sheet metal stamping is a quick and cost-efficient method of producing large volumes of metal parts with consistent accuracy.
Versatility: Sheet metal stamping can be used to produce anything from simple, flat parts to complex, 3-dimensional shapes.
Precision: Sheet metal stamping allows for precise and repeatable results due to the use of die tooling.
Cons of Sheet Metal Stamping
Limited depth: Sheet metal stamping is limited in terms of the depth of parts it can produce. It is typically used for parts that are less than 3 inches deep.
Tooling costs: The cost of developing the necessary dies for sheet metal stamping can be high, especially for more complex shapes.
Material waste: Sheet metal stamping produces material waste in the form of scrap metal.
Deep Draw Stamping
Deep draw stamping is a variation of sheet metal stamping, but it is used for creating parts with greater depth. This process involves stretching a metal sheet over a die and then punching it into a shape using a punch press. Deep draw stamping is commonly used in the production of parts such as fuel cells, pressure vessels, and hydraulic cylinders.
Pros of Deep Draw Stamping
Deep-drawn parts: Deep draw stamping can produce parts with greater depth than sheet metal stamping, making it suitable for applications that require a deeper form.
Minimal material waste: Deep draw stamping produces less scrap material than sheet metal stamping.
Reduced tooling costs: Deep draw stamping requires less tooling compared to sheet metal stamping, making it a cost-effective option for creating parts with greater depth.
Cons of Deep Draw Stamping
Production time: Deep draw stamping is a slower process compared to sheet metal stamping, as the metal sheet requires more shaping and stretching.
Limited versatility: Deep draw stamping is not as versatile as sheet metal stamping, as it is only suitable for parts requiring greater depth.
Difficult to control: Due to the stretching of the metal sheet, deep draw stamping can be difficult to control and requires a higher level of skill from the operator.
Conclusion
In summary, sheet metal stamping and deep draw stamping are both viable options for creating metal parts, depending on the specific requirements of the application. Sheet metal stamping is a more versatile and efficient process that works best for creating flat or shallow 3-dimensional parts quickly and accurately. Deep draw stamping is ideal for creating parts with greater depth, but it is a slower and less versatile process. Ultimately, the decision between sheet metal stamping and deep draw stamping will depend on the requirements of the specific application, as well as the cost and efficiency considerations.